Monitoring of building automation
The main purpose
The main purpose of technical systems monitoring is to provide a professional service, as a result of which the operation of the building’s technical systems is kept as optimal as possible by regularly setting it up and inspecting it. Anomalies and alarms are also monitored, and the maintenance company is notified directly if necessary. The purpose of remote management monitoring is also to release the customer from the obligation to monitor technical systems and to perform fine-tuning and thus try to realize the potential of energy savings to the maximum.
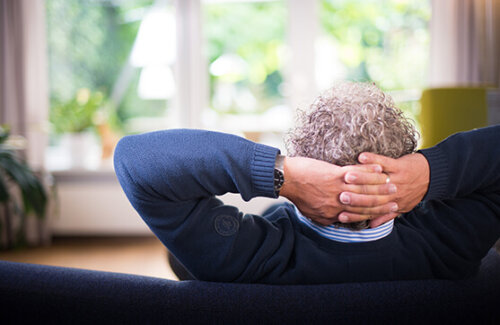
When monitoring of technical systems is needed?
- The building’s technical systems must be monitored regularly to ensure that they function as needed. From time to time it is necessary to make changes or check – working hours, setpoints, correction of various anomalies. In this way, both heat and electricity costs can be kept to a minimum. If there is no need to keep the systems in operation in the customer’s building on weekends and public holidays, the technical systems (eg ventilation) must be switched off if possible or the temperatures/setpoints must be lowered.
- In the absence of a remote management assessment of the condition of the systems, which does not directly impede the operation of the systems but may lead to significant additional costs. For example, incorrect operation of heat recovery, leaks in heating valves, etc.
- If the systems automation has not been thoroughly analyzed and monitored periodically. This is not possible in a few days, but requires a longer period of continuous feedback on the settings. System builders often do not have the time or motivation to deal with this, which can lead to a large amount of energy being lost.
Benefits of monitoring
- Money and energy savings – real payback period less than one year
- Improvement of indoor climate parameters and thus increase of employee productivity
- Extending the life of utility systems and reducing the need for investment
- From continuous fire fighting to preventive action
- Reduction of administrative and repair costs in the long run
- Ensuring transparency in systems and ensuring responsiveness
- Smaller environmental footprint – less greenhouse gas emissions
- Improving the energy label of a building in order to remain in compliance with the established requirements
- Ideas and basic solutions for renovation works
- New ideas to consider when designing and building new buildings
- Additional supervision in terms of maintenance, builder, designer, etc
- Assistance in identifying problems and improving the quality of maintenance
- Timely maintenance and repair planning
- Simplify the introduction of automation changes
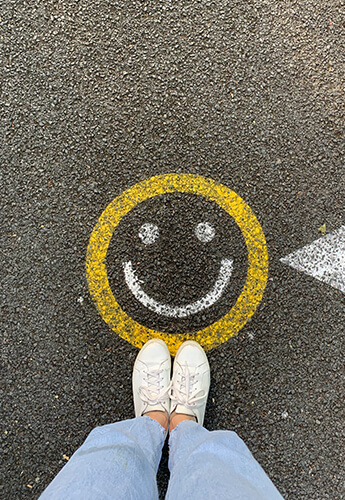
What is done during the monitoring?
- System error messages, work schedules, deviations from setpoints, heat recovery efficiency and anomalies, etc. are monitored periodically.
- Settings are made or helped according to the client’s wishes and possibilities.
- Feedback will be provided on the condition of the systems and suggestions for improvement will be made in order to make the systems more energy efficient. Care will be taken to ensure that the savings do not come at the expense of a good indoor climate.
- System error messages, heating schedules, temperature differences, deviations from setpoints and anomalies, etc. are monitored periodically.
- If possible, heating schedule reductions are set for non-working hours.
- Feedback will be provided on the condition of the systems and suggestions for improvement will be made in order to make the systems more energy efficient. Care will be taken to ensure that the savings do not come at the expense of a good indoor climate.
- System error messages, temperature differences, deviations from setpoints and anomalies, etc. are monitored periodically.
- Various optimization options for refrigeration machines are monitored.
- Make sure that the rooms are not overheated or underheated.
- Care must be taken to ensure that the heating and cooling do not work against each other.
- The operating modes of the devices are monitored and the setting values are adjusted as required.
Standard problems and shortcomings
- Incomprehensible meaning and logic of setpoints, what and how exactly are controlled.
- There are inconsistencies in the control logics of automation and different devices are not subject to control.
- The operation of ventilation equipment serving the same service area is not interconnected, therefore balanced air exchange in the respective (building) part is not ensured.
- In critical spaces (eg operating theaters), the necessary overpressure of the surrounding spaces is not ensured.
- In the visualization, there is a discrepancy in the display of the outdoor air valves of the ventilation equipment and it is not possible to understand whether the valves are closed, open or in an intermediate state.
- Ventilation systems have an unset set speed and only operate at full speed, which results in higher energy consumption. If the nature of the rooms to be served allows, appropriate settings should be made.
- The supply air setpoint temperatures are too high for many units, which causes excessive heat energy consumption and possibly also cooling energy consumption in cooled rooms. In rooms without cooling, the indoor air temperatures may rise too high.
- The devices work continuously under manual control, but could work on a program basis.
- Ventilation system operating hours and productivity out of order. If ventilation equipment does not work while people are indoors, indoor climate problems can occur and the risk of airborne diseases increases. Devices that run continuously but do not need to use too much energy.
- In the visualization of building automation, for example, filters do not have readings of pressure differential sensors. Therefore, it is not possible to estimate the degree of soiling of the filters. Filters that are too dirty can cause excessive pressure loss, which does not guarantee the required ventilation.
- Ventilation systems do not measure or display airflows, making it impossible to assess whether the required airflows are ensured and whether or not air exchange in the building as a whole is balanced.
- Status is not displayed for heating, cooling and humidification valves. As a result, it is not possible to understand whether the systems are working as intended.
- Many simple optimizations have not been carried out by the maintainer, which achieves the greatest savings – precise setting of time programs with exceptions, setting temperatures.
- Building automation in use that is close to the end of its life (e.g. controllers and modules are no longer produced and spare parts are relatively difficult to obtain).
- An existing building automation computer uses an outdated operating system that is no longer upgraded and therefore unsafe. As a result, there is no way to recover later if something happens to the device.